★提携会社 書籍のご案内

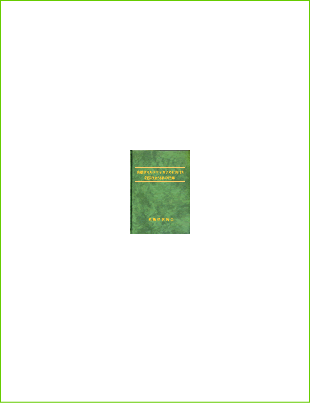

自動車マルチマテリアルに向けた樹脂複合材料の開発
定価 ¥ 88,000(税込)
販売価格 ¥ 88,000(税込)
商品番号:dg0064
ISBN: 978-4-86104-883-8
下記から目次項目単位を選択し、購入目次を設定願います。
■発刊日:2022年5月31日
■販売者:パテントテック社
■出版社:株式会社 技術情報協会
■資料体裁:A4版、680頁
耐衝撃性、耐熱性、耐候性、機械特性、、、 自動車の軽量化と両立するための特性の向上技術について徹底解説!
環境負荷を低減するには? リサイクル性、環境負荷のバランス、LCAを考慮した開発事例を詳解!
■本書のポイント
◆自動車マルチマテリアルと軽量化の動向◆
・自動車車体、部品に求められる材料の強度、耐久性
・樹脂/金属の接合時の強度ばらつきの抑制技術、疲労特性の向上技術
・車両の耐久性、機能性、コスト、リサイクル性、環境負荷のバランス
・LCAを考慮した材料の選定、開発
◆自動車用樹脂材料の力学特性・耐衝撃性の向上◆
・ポリマー材料の力学的特性の向上技術、 高剛性化、高靭性化
・エンジニアリングプラスチックの耐熱性、機械特性の向上
・樹脂材料の発泡技術と衝撃吸収性の向上
・自動車用エラストマーの紫外線への耐候性、耐熱劣化性の対策
・自動車窓、カメラレンズに使用する透明材料の樹脂化
◆繊維複合材料の強度信頼性向上、自動車での応用事例◆
・繊維複合材料の疲労破壊のメカニズムと耐久性の向上技術
・マトリックス樹脂に求められる特性
・繊維複合材料の界面接着性改善、相溶化剤、サイジング剤の利用のポイント
・繊維の均一、等方分散と高せん断成形加工技術
・車体、自動車部品としての応用事例、繊維複合材料に求められる特性
・繊維複合材料の疲労における長期信頼性評価
■執筆者(敬称略)
山根健オフィス | 山根 健 | 金沢工業大学 | 西田 裕文 |
日産自動車(株) | 藤川 真一郎 | 金沢工業大学 | 山下 博 |
(株)本田技術研究所 | 漆山 雄太 | サンワトレーディング(株) | 馬場 俊一 |
東レ(株) | 田中 文彦 | 三井化学(株) | 水本 和也 |
金沢工業大学 | 影山 裕史 | (株)HSPテクノロジーズ | 清水 博 |
マツダ(株) | 髙見 明秀 | (株)栗本鐵工所 | 伊藤 友樹 |
(株)神戸製鋼所 | 鈴木 励一 | 神奈川大学 | 松本 紘宜 |
東京農工大学 | 斎藤 拓 | トヨタ自動車(株) | 安達 善之 |
北陸先端科学技術大学院大学 | 山口 政之 | 住友化学(株) | 佐藤 知広 |
(株)プライムポリマー | 板倉 啓太 | 北川精機(株) | 竹井 宏行 |
(株)スズキ・マテリアル・テクノロジー・ アンド・コンサルティング |
鈴木 孝典 | (株)キャップ | 吉田 透 |
近畿大学 | 白石 浩平 | 東レエンジニアリングDソリューションズ(株) | 山川 耕志郎 |
大洋塩ビ(株) | 榎本 真久 | 名古屋大学 | 山中 淳彦 |
大塚化学(株) | 稲田 幸輔 | 早稲田大学 | 細井 厚志 |
ムーンクラフト(株) | 竹林 康仁 | (地独)京都市産業技術研究所 | 伊藤 彰浩 |
西澤技術研究所 | 西澤 仁 | 金沢工業大学 | 影山 裕史 |
住友ベークライト(株) | 井川 亮一 | トクラス(株) | 大峠 慎二 |
グリーンケミカルズ(株) | 橘 賢也 | 日本ゼオン(株) | 中野 鮎美 |
(公財)地球環境産業技術研究機構 | 乾 将行 | 三井化学(株) | 藤村 太 |
BASFジャパン(株) | 勝又 勇太郎 | 三井化学(株) | 藤村 太 |
(株)クラレ | 關口 健治 | 三井化学(株) | 金子 達雄 |
東洋紡(株) | 岩村 和樹 | 三井化学(株) | 西野 創一郎 |
アルケマ(株) | 尾形 慎太郎 | 北陸先端科学技術大学院大学 | 金子 達雄 |
(株)カネカ | 三枝 一範 | 茨城大学 | 西野 創一郎 |
DIC(株) | 神田 智道 | 日本アレックス(株) | 遠山 達也 |
ポリプラスチックス(株) | 田口 吉昭 | (株)タマリ工業 | 三瓶 和久 |
秋元技術士事務所 | 秋元 英郎 | 近畿大学 | 西籔 和明 |
(株)日本製鋼所 | 油布 拓也 | 神戸市立工業高等専問学校 | 田邉 大貴 |
サンユレック(株) | 上野 健一 | 横浜ゴム(株) | 木村 和資 |
積水化成品工業(株) | 大脇 皓樹 | 鈴木接着技術研究所 | 鈴木 靖昭 |
ENEOS(株) | 知野 圭介 | 大成プラス(株) | 板橋 雅巳 |
TPEテクノロジー(株) | 西 一朗 | 長岡技術科学大学 | 倉橋 貴彦 |
名古屋大学 | 梶田 貴都 | JFEスチール(株) | 斉藤 孝信 |
名古屋大学 | 野呂 篤史 | 明治大学 | 萩原 一郎 |
同志社大学 | 藤井 透 |
◇第1章 マルチマテリアルと自動車の軽量化動向◇
第1節 自動車車体軽量化のための材料開発と接合技術動向
1.車両重量の変遷
2.軽量化のニーズ
3.自動車材料の変遷
3.1 鉄系材料
3.2 軽金属系材料
3.3 樹脂系材料
4.マルチマテリアル
5.製造技術、接着
5.1 鉄鋼車体の製造技術
5.2 非鉄金属車体の製造技術
5.3 BMWの開発したCFRPモノコック製造プロセス
5.4 接着
6.塗装他表面保護と加飾
第2節 車両軽量化のための材料・加工技術
1.車両軽量化の目的と方策
2.鋼板の高強度化
2.1 ハイテン材の採用
2.2 ホットスタンピング
2.3 車両へのアルミニウムの採用
2.3.1 板材・形材・接合
2.3.2 鍛造材
2.3.3 鋳造材
2.3.4 樹脂材料
第3節 自動車軽量化に向けた複合材料樹脂の開発
1.自動車における軽量化のニーズとFRP
2.FRPの適用と技術蓄積
2.1 1950年代 草創期とFRP骨格適用
2.2 2003年 実用CFRP骨格のひな形
2.3 作り生産性とボデー,部品化技術
2.4 マルチマテリアルボデー
2.5 シャーシ部品への応用
3.自動車構造材としてFRP の活用にむけて
3.1 FRPにおける設計コンセプト構築とビルディング・ブロック・アプローチ
3.2 ミクロスケールとメゾスケール
3.3 CFRP構造物の強度とマクロ特性
3.4 マルチマテリアルとデザインデマンド
4.社会と自動車の変革期を迎えて
第4節 自動車用途に向けた炭素繊維と炭素繊維複合材料の開発動向
1.自動車の軽量化動向
2.炭素繊維の最新動向
2.1 需要動向
2.2 技術動向
2.2.1 各国動向
2.2.2 企業動向
3.炭素繊維複合材料の動向
3.1 複合材料の基礎
3.2 成形法の基礎
3.2.1 シートモールディングコンパウンド
3.2.2 射出成形
3.2.3 長繊維強化熱可塑性樹脂の直接成形
第5節 セルロースナノファイバーを活かしたクルマづくり
1.将来のクルマを取り巻く環境の変化
1.1 二つのキーワード
1.2 多目的モビリティへの要求拡大
2.モビリティ材料への要求
2.1 軽量材料への期待
2.2 軽量材料の課題
2.3 LCA観点の必要性
3.CNF強化複合材料(CNFRP)への期待と課題
3.1 CNFRPへの期待
3.1.1 バイオマスFRP(BFRP)の現状と課題
3.1.2 CNFRPの意味と期待
3.2 CNFRPへの挑戦(NCVプロジェクト)
3.2.1 環境省NCVプロジェクト
3.2.2 NCVプロジェクト開発を通して分かったこと(部品化の可能性 )
3.2.3 NCVプロジェクト開発を通して分かったこと(更なる素材開発の方向性 )
4.CNF強化複合材料(CNFRP)の今後
4.1 質の改善
4.1.1 材料設計
4.1.1.1 CFRPマトリックス樹脂やバイオマス樹脂とのコラボ
4.1.1.2 CNFの機能性を活かす
4.1.2 部品設計
4.1.2.1 CFRPとのコラボ
4.1.2.2 他の等方性材料(金属等)とのコラボ
4.1.3 車両設計
4.1.4 信頼性確保
4.2 量の改善
4.2.1 自然との融合
4.2.1.1 移動時のCO2排出量の低減
4.2.1.2 素材製造時のCO2排出量の低減
4.2.1.3 部品・製品製造時のCO2排出量の低減
4.2.1.4 廃棄時のCO2排出量の低減
4.2.2 地域との融合
第6節 マルチマテリアル化車体の動向と異種材料接合技術
1.車体のマルチマテリアル化
2.マルチマテリアル化を実現する異材接合技術
2.1 接合技術動向
2.2 接合技術
2.2.1 摩擦攪拌点接合
2.2.1.1 摩擦攪拌点接合
2.2.1.2 アルミニウム/鋼板の摩擦攪拌点接合
2.2.1.3 樹脂(CFRPなど)/アルミニウムの摩擦攪拌点接合
2.2.1.4 評価解析技術
2.2.1.5 異材点接合の適用想定
3.まとめと今後の課題
第7節 バッテリーケース構体のマルチマテリアル化への挑戦
1.電気自動車の歴史と世界的動向
2.電池の短所とバッテリーケースの機能
3.バッテリーケースの構造
4.バッテリーケースの材質
5.(株)神戸製鋼所提案のマルチマテリアルバッテリーケースと異種材接合技術EASW
6.今後の見通し
◇第2章 熱可塑性樹脂の剛性、耐候性の向上と 自動車部材の開発 ◇
第1節 ポリマー材料の構造と力学的性質
1.非晶性ポリマー
2.結晶性ポリマー
3.ゴム
4.ポリマー発泡体
5.ポリマーブレンド
第2節 分子配向の制御によるポリプロピレンの高性能化
1.高剛性化
1.1 シシカバブ構造の形成
1.2 結晶核剤による分子配向の顕在化
2.高靭性化
2.1 軟質材料の添加
2.2 β晶結晶による高靭性化
2.3 結晶核剤の利用によるベニヤ板構造の形成
第3節 ポリプロピレンの自動車部材への応用と樹脂開発の取り組み
1.PPおよびPPコンパウンド材の自動車部材への展開概況
2.自動車向けPPの樹脂開発
2.1 高立体規則性・高流動PP
2.2 ブロックPP
2.3 高ゴム量含有高立体規則性ブロックPP
3.サーキュラーエコノミー社会に貢献する製品・材料開発
3.1 射出発泡成形体
3.2 外板材(高剛性・低線膨張性材料)
3.3 繊維強化PP
4.今後の展望
第4節 PVDFの特徴と自動車分野への応用
1.PVDFの特徴
1.1 PVDFの化学的・物理的性質
1.2 PVDFの重合法による物性の違い
2.PVDFの用途
2.1 歴史的な変遷
2.2 市場規模
3.車載用途への展開
3.1 フッ素樹脂コーティングチューブ
3.2 ヒートシュリンクチューブ
3.3 リチウムイオン電池バインダー
3.4 デコラティブフィルム
3.5 センサー
第5節 バイオプラスチックポリ乳酸の複合化による自動車部品の開発
1.L-PLAの耐熱性改善
1.1 L-PLA-0.1wt%澱粉共重合樹脂の合成とステレオコンプレックス形成による耐熱性改善
1.2 D - COPLA樹脂を用いたL- PLAの耐熱性改善
1.3 セルロース微粉末の配合によるL- PLA耐熱性改善
2.L- PLAの耐熱性と耐衝撃性の同時改善
3.結晶化促進/相溶化セグメントをもつブロックポリマーによるL- PLA耐熱・耐衝撃性の改善
4.ポリビニルアルコール(PVA)繊維の配合による耐衝撃性ならびに耐熱性の改善
5.L- PLAの耐熱性と耐衝撃性を改善するD ? COPLA改良型の結晶核剤の調製と物性
6.天然ゴム(NR)の配合によるL- PLAの耐衝撃性と加水分解性の改善
6.1 NRの配合によるL- PLA物性への影響
6.2 エポキシ化天然ゴム(ENR)及びNR配合によるL- PLA物性への影響
6.3 NRとENRの量比とNR用老化防止剤の添加が及ぼす物性への影響
7.ポリカルボジイミド(加水分解抑制剤)添加に及ぼす分子量の検討
第6節 PVCの高耐久化技術と自動車部材での応用
1.PVC(ポリ塩化ビニル)とは
1.1 PVCの産業連関
1.2 PVCの環境負荷 ~LCIデータおよびマテリアルリサイクル率~
1.3 PVCの製造(重合)方法
1.4 PVCの構造と特徴
1.4.1 PVCの結晶構造、高次構造
1.4.2 可塑剤によるPVCの可塑化機構
1.4.3 PVC加工品の特徴
1.5 PVCの自動車部材用途への動向
2.PVC加工品の高耐久化技術と自動車部材への適用
2.1 PVCの高重合度化、共重合化による加工品の高耐久化
2.2 可塑剤の選定による加工品の高耐久化
2.3 ゴム粒子分散による加工品の高耐久化
第7節 超微細チタン酸カリウム繊維を配合した樹脂複合材料の開発
1.チタン酸カリウム繊維:ティスモ、樹脂複合材料:ポチコンに関して
2.自動車向け射出成型部品の使用事例
3.マルチマテリアル化による高比強度材料開発
3.1 開発の背景
3.2 CFRTP不織布について
3.3 ポチコンのフィルム化
3.4 マルチマテリアル化
4.今後の展開
第8節 「しなやかなタフポリマー」を活用したコンセプトカーの開発
1.コンセプトカー開発のポイント
1.1 研究の背景と経緯
1.2 研究の内容
2.スタイリングデザイン
2.1 モノコックボディ
2.2 サスペンション
2.3 窓材料
2.4 タイヤ・ホイール
2.5 クラッシュボックス
2.6 バッテリーパック
2.7 インテリア
2.8 その他の特徴
3.温室効果ガス(GHG)削減効果
4.走行試験
5.他用途への応用
第9節 高分子材料の難燃化と難燃材料の自動車分野への応用
1.自動車用材料の難燃性規格と要求性能
2.高分子材料の難燃化技術と難燃材料の特性
2.1 難燃化のメカニズム
2.2 高難燃効率と環境安全性を目指す自動車材料の難燃化技術
2.3 難燃剤の種類と選択
3.最近の難燃性低誘電特性樹脂材料の開発
3.1 自動運転、5G通信対応低誘電特性難燃材料に要求される特性と開発の考え方
◇第3章 熱硬化性樹脂の開発、剛性、 機械強度性向上と自動車での応用 ◇
第1節 熱硬化性樹脂長繊維成形材料の射出成形対応化によるフェノール樹脂成形材料の耐熱性向上と自動車部材への応用
1.熱硬化樹脂成形材料の特長
1.1 熱硬化性樹脂と熱可塑性樹脂
1.2 ガラス繊維強化フェノール樹脂成形材料
2.熱硬化性樹脂長繊維成形材料の現状と課題
2.1 長繊維材の製造方法
2.2 自動車用途へ展開するための長繊維材の課題
3.熱硬化性樹脂長繊維成形材料の射出成形技術
3.1 長繊維材射出成形品中の繊維長と分散性の理想状態評価
3.2 繊維長と衝撃強さ
3.3 繊維長と分散性の関係
3.4 繊維長、分散性、試験片強度とばらつきの関係
3.5 長繊維材射出成形試験片における繊維長・分散性の理想状態
3.6 射出成形機仕様、可塑化条件の繊維長に対する影響
3.7 長繊維材射出成形中の繊維異方性
4.熱硬化性樹脂ガラス長繊維成形品の特長と今後の展望
4.1 熱硬化性樹脂ガラス長繊維材の特長
第2節 植物由来フェノール樹脂の開発と自動車での応用
1.自動車部品向け用途例
1.1 成形材料
1.2 摩擦材
2.植物由来フェノールの量産化技術
2.1 フェノールの植物由来化の重要性
2.2 バイオプロセスの生産性向上
2.2.1 高生産性RITEバイオプロセス
2.2.2 2段工程法
2.3 濃縮精製プロセスの開発
2.4 パイロット設備での実証
2.5 植物由来フェノール樹脂の特長
◇第4章 エンジニアリングプラスチックの開発と 耐衝撃特性向上 ◇
第1節 機械特性に優れるUltramidRの開発とそれを利用した金属部品の樹脂化
1.樹脂化の必要性およびメリット
1.1 ポリアミド製シート後部補強材(トヨタ・シエナハイブリッド2021年モデル)
1.1.1 適用部品
1.1.2 なぜ熱可塑性樹脂で金属を代替するのか
1.1.3 BASFの高強度ポリアミド材UltramidRシリーズ
1.1.4 樹脂化のメリット
1.1.5 BASFの独自CAEシステムUltrasimRによる設計のサポート
1.1.6 シート構造部品の樹脂化における課題
1.1.7 樹脂化の効果
1.2 ポリアミドをオーバーモールドしたポリウレタンコンポジット製トンネル補強材(ジープ・グランドチェロキー2021モデル)
1.2.1 適用部品
1.2.2 連続繊維コンポジット材をエンジニアリングプラスチックにインサート成形
1.2.3 引き抜き成形コンポジット材に特化したポリウレタンシステムElastocoat(R) 74850
1.2.4 コンポジット材への高精度CAE解析
1.2.5 業界初のイノベーションとBASF材のメリット
第2節 高耐熱性ポリアミド樹脂<ジェネスタ>PA9Tの特性と自動車部材への応用
1.耐熱性ポリアミドの歴史
2.耐熱性ポリアミド<ジェネスタ>について
3.車載電装用途
3.1 電動車の高電圧化
3.2 耐トラッキング性
3.3 PA9T<ジェネスタ>の耐トラッキング性
4.燃料電池車用途
5.樹脂配管用途
5.1 燃料配管用途
5.2 冷却配管用途
5.3 押出成形技術・CAE
第3節 発泡成形用高機能ポリアミド樹脂の開発
1.PAの発泡成形品で得られる軽量化設計のメリット
2.PAの発泡成形における課題
2.1 射出発泡成形
2.1.1 ショートショット法
2.1.2 コアバック法
2.2 発泡剤
2.2.1 化学発泡剤
2.2.2 超臨界流体を含む物理発泡剤
2.2.3 熱膨張性マイクロカプセル
3.射出発泡成形用ポリアミド樹脂の設計
3.1 射出発泡成形用樹脂に求められる特性
3.2 粘度調整手法
3.3 結晶化温度調整手法
4.射出発泡成形用グレードの特徴
4.1 発泡成形性向上への効果
4.2 ガラス繊維強化グレードへの応用
4.3 セルが均一に微細化されたコアバック発泡成形品の特性
4.3.1 耐荷重特性
4.3.2 耐振動特性
4.3.3 断熱特性
4.3.4 衝撃特性
第4節 ヒマシ油由来ポリアミドの自動車用途への展開
1.ポリアミドとは
2.ヒマシ油からモノマー
3.ヒマシ油由来脂肪族ポリアミド
3.1 ポリアミド11
3.1.1 燃料チューブ
3.1.2 冷却水配管
3.1.3 燃料電池自動車に関わる用途
3.1.4 その他
3.2 ポリアミド610
3.3 ポリアミド1010、ポリアミド1012
3.4 ポリアミド410
4.ヒマシ油由来半芳香族ポリアミド
4.1 PA10T
4.2 ポリアミド10T/11
5.ヒマシ油由来特殊ポリアミド
5.1 植物由来透明ポリアミド
5.2 植物由来ポリアミドエラストマー
第5節 自動車外装用ポリカーボネート系アロイ射出成形材料の発泡技術
1.ポリカーボネート/ポリエチレンテレフタレート系ポリマーアロイの特徴
2.自動車部材の軽量化・材料使用量の低減技術
2.1 薄肉化の課題
2.2 発泡技術
2.2.1 ポリカーボネート系樹脂における発泡剤の選択
2.2.2 熱膨張性マイクロカプセルの概要
2.2.3 成形方法
2.2.4 熱膨張性マイクロカプセルマスターバッチ
2.2.5 熱膨張性マイクロカプセルマスターバッチの改良
2.2.6 取扱時の注意事項
2.3 発泡を伴う自動車外層部材の設計
第6節 PPSの自動車への適用
1.自動車用途への適用
1.1 市場状況と需要動向
1.2 自動車部品の適用事例
1.2.1 各種車載センサー
1.2.2 点火コイルケース
1.2.3 IPM
1.2.4 電流センサー、DC/DCコンバータ等
1.2.5 電池ガスケット
2.技術動向
2.1 耐冷熱衝撃性の改良
2.2 絶縁高熱伝導性材料
2.3 押出成形(チューブ/パイプ)部品への適用
2.4 摺動部品への適用
2.5 EMC対応部品への適用
第7節 エンプラファインパウダーの開発と自動車分野への応用展開
1.エンプラとは
2.開発の経緯
3.エンプラファインパウダーの特長
4.自動車分野への応用展
◇第5章 自動車での利用に向けた樹脂の発泡技術◇
第1節 車体軽量化のための発泡成形技術
1.発泡による軽量化の考え方
1.1 発泡体の構造
1.2 発泡体の特徴
2.発泡成形とは
2.1 発泡成形のプロセス
2.2 発泡成形に用いる発泡剤
2.2.1 化学発泡剤
2.2.2 物理発泡剤
2.2.3 超臨界流体
2.2.4 膨張性マイクロカプセル
2.3 発泡成形の種類
2.3.1 ビーズ発泡成形
2.3.2 プレス発泡成形
2.3.3 常圧二次発泡成形
2.3.4 射出発泡成形
2.3.5 押出発泡成形
2.3.6 発泡ブロー成形
3.微細射出発泡成形
3.1 微細発泡の基本原理
3.2 微細射出発泡成形
3.3 微細射出発泡成形の利点
4.コアバック法
4.1 コアバック法の金型動作
4.2 コアバック法による軽量化効果
第2節 高圧ガス発生装置が不要な物理発泡成形技術「SOFIT(R)」と自動車部品への展開
1.概要
2.特長
2.1 ガス溶解量の従来技術との比較
2.2 ソリ低減効果
2.3 成形安定性
3.自動車部品への展開
3.1 エンプラ、スーパーエンプラの成形
3.2 複合成形、多色成形への展開
第3節 エポキシ樹脂の発泡技術とCFRP用プリプレグ材料、その可能性
1.エポキシ樹脂とは
1.1 エポキシ樹脂、その用途
1.1.1 土木・接着・塗料分野
1.1.2 電気・電子分野
1.1.3 複合材料
2.エポキシ樹脂発泡技術
2.1 発泡による利点
2.2 発泡化の手法
2.2.1 エポキシの重合による発泡
2.2.2 発泡剤による発泡
2.3 発泡させるときの注意点
3.CFRP用プリプレグ材料
3.1 CFRPの利点
3.2 熱硬化樹脂プリプレグ材料
3.2.1 エポキシプリプレグ材料
3.2.2 ビスマレイミドプリプレグ材料
3.3 熱可塑樹脂プリプレグ材料
3.4 繊維材料
3.4.1 炭素繊維
3.4.2 その他繊維
4.軽量化への応用
4.1 自動車分野
4.2 モビリティ分野
4.3 ウエアラブル
4.4 産業機器
4.5 スポーツ分野
第4節 耐衝撃性に優れるポリスチレン・ポリオレフィン複合樹脂発泡体の開発
1.ピオセランの構造
1.1 内部構造の制御
1.2 内部構造
2. ピオセランの特徴
2.1 ピオセランのポリオレフィン種と物性の関係
2.2 ピオセランの諸物性
3.ピオセランの機能性向上手法
3.1 内部構造制御
3.2 ポリオレフィン種の改質事例
3.3 ピオセラン開発事例紹介
3.3.1 発泡体の高発泡化によるリスク
3.3.2 高発泡化可能な難燃性ピオセランの物性
4.自動車部材への応用
5.ピオセランのリサイクル
◇第6章 自動車用エラストマーの開発と 強度、耐候性の向上 ◇
第1節 低硬度かつ低圧縮永久歪性を有するオレフィン系エラストマー
1.新開発エラストマーについて
1.1 特徴
1.1.1 低硬度・低圧縮永久歪性
1.1.2 加硫ゴム並みの機械特性
1.1.3 フィラー・樹脂・他ポリマーとの混合、および2色成形加工
1.1.4 物性比較まとめ
1.2 一般グレードラインナップ
1.3 特殊グレード
1.3.1 軟質・高流動グレード
1.3.2 高耐熱・接着グレード
1.3.3 導電グレード
1.4 加硫ゴムへの配合
1.5 性能発現メカニズム
1.6 成形方法
1.6.1 射出成形
1.6.2 押出成形
1.6.3 プレス成形
2.用途展開と今後の展望
第2節 熱可塑性エラストマーの耐候性向上と自動車での応用
1.エラストマー概要
1.1 熱可塑性エラストマー(TPE)
1.2 非熱可塑性エラストマー
2.エラストマーの耐候性
3.エラストマー各論
3.1 オレフィン系熱可塑性エラストマー(TPO)
3.1.1 概要
3.1.2 対策
3.2 エステル系熱可塑性エラストマー(TPC)
3.2.1 概要
3.2.2 対策
3.3 ウレタン系熱可塑性エラストマー(TPU)
3.3.1 概要
3.3.2 対策
3.4 アミド系(TPAE)
3.5 シリコーン系(非熱可塑性)
◇第7章 ガラス・炭素繊維複合材料の靭性向上、 密着性改善技術と自動車部材の開発 ◇
第1節 ガラス繊維およびカーボン繊維強化複合材料の破壊と耐久性
1.F-PMCとは?
1.1 多種・多様な強化繊維
1.2 多種・多様な樹脂
1.3 多種・多様なF-PMC
2.F-PMC構造物の破壊と設計
2.1 基礎データ
2.2 F-PMCの性能
2.3 F-PMCの破壊と設計
3.ガラス繊維およびカーボン繊維強化複合材料は疲労する
4.二つの疲労
4.1 繰り返し(変動)荷重下での疲労と寿命
4.2 静疲労
4.3 金属材料の疲労
5.F-PMCの疲労破壊を考える場合の難しさ
5.1 F-PMCの典型的構造と内部応力、可能性のある破壊起点
5.2 強化繊維と90°方向の引張り強度は極端に小さい
6.強化繊維は疲労するか?
6.1 ガラス繊維の疲労
6.2 カーボン繊維の疲労
6.3 母材(樹脂)の疲労
7.均一材料の疲労破壊メカニズム
8.F-PMCの疲労特性
8.1 疲労寿命に影響を及ぼす要因
8.2 一方向GFRP
8.3 多方向積層板
8.4 SMCの疲労
9.炭素繊維の疲労強度を向上させる
9.1 平織炭素繊維強化FRPの疲労破壊プロセス
9.2 平織CF/EP-PMCの疲労寿命を増すには?
9.3 微細繊維による母材樹脂の物理的変性、細くて長ければよい?
9.4 微細繊維、なぜ耐久性は上がる?
10.耐久性に強く影響する吸湿/湿気
第2節 CFRPのマトリックス樹脂の開発動向
1.合成樹脂の分類
2.熱硬化性樹脂の種類と特徴
2.1 エポキシ樹脂
2.2 ジシクロペンタジエン(DCPD)樹脂
3.現場重合型熱可塑性樹脂の種類と特徴
3.1 連鎖重合型と逐次重合型
3.2 結晶性と非晶性
4.動的共有結合含有熱硬化性樹脂の種類と特徴
第3節 相溶化剤を用いたポリプロピレンと炭素繊維の界面接着性の改善
1.相溶化剤
1.1 無水マレイン酸変性ポリプロピレン
1.2 イソタクチックポリプロピレン-ポリアクリル酸共重合体
2.相溶化剤を添加したPP/相溶化剤樹脂の作製
3.界面接着性の評価
3.1 フラグメンテーション試験(Fragmentation test:FT)
3.2 マイクロドロップレット試験(Micro-Droplet test:MD)
4.結晶性の評価
5.相溶化剤を添加したCFRPの力学物性
5.1 PP/相溶化剤とCFの複合化
5.2 引張試験
5.3 シャルピー衝撃試験
第4節 連続繊維熱可塑性複合材料の自動車部品への適用
1.連続繊維熱可塑性複合材料
1.1 CFRTP・GFRTPの異方性
1.2 コンソリデーション
1.3 Tepex種類
2.成形プロセス
2.1 ハイブリッド成形
2.2 IR(赤外線) ヒーター
3.自動車部品への適用
3.1 ドアモジュール
3.2 フロントエンド
3.3 A ピラー
3.4 ブレーキペダル
3.5 アンダーカバー
3.6 ヒンジ
4.CFRTPとGFRTPの比較
5.今後の適用部品
5.1 大型バッテリーハウジング
5.2 バッテリーブランケット
第5節 ポリプロピレンをマトリックスとした熱可塑性炭素繊維強化材料の自動車部材開発
1.一方向連続炭素繊維強化PPシートの特徴と用途
2.マルチマテリアル部品の事例
2.1 バンパービーム
2.2 バックドア
3.接着接合
第6節 高せん断成形加工法により作製した炭素繊維が均一かつ等方的に分散・配置したCFRTP
1.高せん断成形加工法の概要
2.高せん断加工によるフィラーのナノ分散化
3.新規なCFRTP材料
4.CFRTP材料の評価における留意点
第7節 繊維強化熱可塑性樹脂の直接成形技術~Carbon-LFTDシステムの開発~
1.Carbon-LFTDプロセス
1.1 溶融・混練工程
1.2 裁断・保温工程
1.3 金型への材料投入・成形工程
2.Carbon-LFTDシステムの特長
2.1 成形品の高強度化
2.2 材料コストの低減
2.3 成形材料の循環利用
3.成形事例
第8節 CFRTPの軽量構造体の成形及び異種材接合技術、ナノ繊維を用いた新規接合技術
1.FRTPの軽量構造体の成形技術
1.1 FRTPの中間基材と成形性・オーバーモールド成形法
1.2 オーバーモールド法における融着接合の原理
2.マルチマテリアル化のための異種材接合技術
3.繊維強化プラスチック複合材料へナノ繊維を添加する意義と接合技術へのナノ繊維の適応
3.1 マルチスケール複合材料とナノ繊維による複合材料の選択的強化
3.1.1 ナノ繊維添加FRP
3.1.2 ナノ繊維添加FRTP
3.2 接合技術におけるナノ繊維の応用
3.2.1 接着接合における接着剤へのナノ繊維の添加
3.2.2 3Dプリンター
3.2.3 射出オーバーモールド
第9節 CFRPを用いたクロージャーパネルの開発
1.開発背景
1.1 自動車における軽量化の重要性
1.2 これまでのCFRP開発
1.3 車両企画
2.技術開発
2.1 軽量化の考え
2.2 製法の比較・材料選定
2.3 CFRPの特徴を活かした開発~マルチマテリアルボデー
3.構造検討
3.1 設計検討
3.2 重点補強部位選定~R/F部形状
3.3 接着構造
3.4 リブによる部分補強
4.CFRP化による効果
4.1 軽量化効果
4.2 コスト効果
4.3 低重心化効果
4.4 後方視界の拡大
5.生産技術
5.1 生産拠点
5.2 ボデー工程
5.3 プレス工程(成形)
5.3.1 CFRP成形
6.今後の展望と課題
6.1 新車CO2ゼロ
6.2 ライフサイクルCO2ゼロ
第10節 液晶ポリマー系繊維強化コンパウンドの特性と自動車部品への応用
1.液晶ポリマーの特徴
2.液晶ポリマーの用途
3.液晶ポリマーの自動車用途における採用例
3.1 電装部品
3.2 オイルパイプへの展開
3.3 その他用途への展開の可能性
4.新規長繊維強化コンパウンド
4.1 高剛性CF強化グレード(SCG-380A)
4.2 破壊時衝撃吸収能に優れるGF強化グレード(SCG-379)
4.3 金属並みの電磁波シールド特性を有するCF強化グレード(SCG-405)
5.自動車部品としての性能評価
6.液晶ポリマーの自動車用途への展開においての課題
6.1 材料コスト
6.2 他部材との接合技術
6.3 シミュレーション手法の開発
第11節 熱可塑性CFRP一方向(UD)連続維繊積層板の量産技術
1.UD-CFRTP積層板成形装置
1.1 CFRTP自動積層装置
1.1.1 切断接合部
1.1.2 積層部
1.2 多段プレス装置による積層成形
1.3 CFRTPスタンピング成形一貫生産ライン
第12節 熱可塑性CFRPのヒートアンドクール成形技術と射出成形技術
1.CFRTPのプレス成形技術の概要
2.通電抵抗加熱金型の原理
3.TAM成形システムの構成
4.通電抵抗加熱金型の温度予測
5.ヒートアンドクール金型による熱プレスの利点
6.TAM成形法によるCFRTPのプレス成形プロセス
7.TAM成形法で成形できるCFRTP材料
8.ランダムコンプレッション成形
9.熱可塑性UDテープ
第13節 樹脂成形CAE “3D TIMON” による複合材ソリューション
1.射出成形
1.1 繊維強化樹脂を射出成形する際の課題
1.2 繊維配向解析
1.3 残留応力解析
1.4 構造解析との連携
2.プレス成形
2.1 複合材料プレス成形の課題
2.2 長繊維の挙動予測
3.RTM(Resin Transfer Molding)成形
3.1 RTM成形の課題
3.2 RTM成形シミュレーション
第14節 CFRTPの繊維長、繊維配向、繊維分散性分析技術
1.非連続炭素繊維強化熱可塑樹脂系複合材料(D-CFRTP)の最近の技術動向
2.非連続炭素繊維強化熱可塑樹脂複合材料の繊維長分布測定方法
2.1 スキャナーを用いた繊維長分析方法
2.1.1 従来技術の問題点
2.1.2 高解像度スキャナーの利用による効果と問題点
2.2 繊維長分布測定前の試料調製法
2.2.1 従来の試料調製法の問題点
2.2.2 多段階希釈による試料調製法
2.3 繊維長分布分析のまとめ
3.X線回折を利用した非連続炭素繊維強化熱可塑樹脂複合材料の繊維配向分析
3.1 X線回折を利用したCF配向分析法構築の背景
3.2 CF及び一方向強化CFRTP, 織物強化CFRTPのX線回折パターン
3.3 XRDを用いたD-CFRTPの繊維配向分析
3.3.1 D-CFRTPから切り出された引張試験用試験片のXRDパターン
3.3.2 配向方向と配向分布及びこれらと引張特性との関係
3.4 XRDによるD-CFRTPの繊維配向分析法に関するまとめ
4.画像解析による繊維分散状態の評価方法
4.1 CFRTPの繊維分散状態の観察方法
4.2 繊維分散状態が異なるD-CFRTPに対する分散性指標化手法の適用例
4.2.1 繊維分散状態が異なるD-CFRTPの断面画像について
4.2.2 繊維分散状態指標化手法
4.2.3 繊維分散状態指標化法適用結果
第15節 繊維強化複合材料の疲労における長期信頼性評価
1.試験材料
2.試験条件
3.疲労寿命評価手法
3.1 疲労寿命予測モデル
4.結果および考察
4.1 静的試験
4.2 疲労試験
4.3 Epaarachchi and Clausenモデル
4.4 等寿命線図
◇第8章 セルロースナノファイバー複合材料の 強度信頼性向上と自動車構造部材の開発 ◇
第1節 セルロースナノファイバー強化プラスチックの発泡成形
1.CNF強化プラスチックについて
2.ASA変性CNF強化HDPE系の事例紹介
2.1 ASA変性CNF強化プラスチックについて
2.2 ASA変性CNF強化HDPEのバッチ式物理発泡成形
3.アセチル化CNF強化ポリアミド系の事例紹介
3.1 アセチル化CNF強化PA6とその発泡成形について
3.2 熱可塑性エラストマーへの展開
4.アセチル化CNF強化PP発泡体とフィルムインサート成形との組合せ
第2節 RTM成形によるCNF製大型自動車部材の開発
1.RTM成形の特徴
2.RTM成形と自動車の動向(期待と課題)
3.RTM成形とCNF材料の相性
4.CNF製大型RTM成形自動車部品の試作(環境省NCVプロジェクト)
4.1 RTM成形法による大型エンジンフードの試作
4.1.1 設計面への配慮と知見
4.1.2 生産面への配慮と知見
4.2 VaRTM成形法による大型フロアの試作
4.2.1 設計面への配慮と知見
4.2.2 生産面への配慮と知見
5.CNF製大型RTM成形自動車部品の評価(環境省NCVプロジェクト)
5.1 RTM製大型エンジンフードの評価
5.2 VaRTM製大型フロアの評価
6.今後の期待と課題
第3節 耐衝撃性に優れたCNF含有ウッドプラスチックコンポジットの開発
1.WPCの概要
1.1 WPCの歴史
1.2 WPCの一般的な特性
1.3 WPCの原材料
1.4 WPCの製造方法
1.5 WPCの用途
1.6 無機フィラー充填プラスチックとの比較
2.CNFのWPCへの応用
2.1 CNFを添加したWPC
2.2 CNF含有木粉の利用
2.3 CNF-木粉ハイブリッドWPC「ウッドナノプラス」
◇第9章 自動車用透明樹脂の開発と 耐候性、耐熱性の向上 ◇
第1節 透明ナノポリマーアロイの開発と自動車用窓材料への利用可能性
1.高せん断成形加工技術の開発とその概要
2.PC/PMMA透明ナノポリマーアロイの創製
3.PC/PMMA透明ナノポリマーアロイの自動車用窓材料等への利用可能性
3.1 自動車用窓材への利用可能性
3.2 各種透明パネル等への利用可能性
第2節 車載カメラレンズ用シクロオレフィンポリマーの開発と耐熱性向上
1.シクロオレフィンポリマー(COP)の基本特性と光学レンズへの展開
1.1 COPの合成
1.2 COPの光学レンズへの展開
2.シクロオレフィンポリマー(COP)の高耐熱化
2.1 光学レンズ高耐熱化の背景
2.2 添加剤配合設計による高耐熱化
2.2.1 添加剤による高分子劣化抑制
2.2.2 酸化防止剤の変色について
2.3 ポリマー設計による高耐熱化
3.シクロオレフィンポリマー(COP)の車載カメラレンズへの展開
3.1 車載カメラレンズ用ZEONEX(R)T62Rの開発
3.2 ZEONEX(R) T62Rの基礎物性と耐熱性
第3節 環状オレフィン系樹脂の高機能化と車載カメラレンズへの展開
1.光学用プラスチック材料
2.環状オレフィン共重合体「アペル(R)」の特徴
2.1 合成方法と化学構造
2.2 基本物性と光学物性
2.3 アペル(R)の光学銘柄
2.4 イメージセンサーレンズ用途への展開
3.車載カメラレンズ
3.1 車載カメラレンズ市場
3.2 車載カメラレンズ用途に向けた銘柄開発
3.3 耐熱試験における耐黄変性
4.透明性および耐光性の付与による高機能化
第4節 ガラス代替に向けた透明バイオプラスチックの開発
1.バイオプラスチック原料の分子設計
2.バイオベースポリイミドの開発
2.1 高耐熱バイオベースポリイミドの合成
2.2 屈曲型バイオベースポリイミドへの応用
2.3 バイオベースポリイミドの側鎖変換による難燃化
3.バイオベースポリアミドの開発
3.1 高強度バイオベースポリアミドの合成
3.2 バイオベースポリアミドナノ薄膜への応用
◇第10章 マルチマテリアルに向けた 接着接合技術の開発 ◇
第1節 自動車におけるマルチマテリアル化と加工・接合技術
1.熱可塑性CFRPの曲げ成形性と製品強度に及ぼす加工温度の影響1)
1.1 温間曲げにおける供試材と実験方法
1.2 温間曲げ試験の結果とCTスキャンによる断面観察
2.アルミニウム合金と鋼の抵抗スポット溶接における接合メカニズムの解明と強度評価2)
2.1 供試材および実験方法
2.2 せん断引張試験結果
2.3 接合部の断面観察
2.4 鉄鋼/アルミニウム合金接合における金属間化合物
2.5 せん断引張試験における破壊箇所の断面観察
第2節 赤外線を使用した異種材料の接合技術
1.樹脂カシメの工法について
2.赤外線カシメとは
3.赤外線カシメのプロセス
4.他工法と比較した場合の赤外線カシメの特徴
4.1 ワークへのダメージ
4.2 ランニングコスト
4.3 サイクルタイム、ダウンタイム
4.4 カシメ強度と安定性
4.5 安全性
4.6 生産性
4.7 クリーン度
5.赤外線カシメを使用する場合の注意点、設計について
6.赤外線カシメに適したアプリケーション例
7.装置の構成と主な機能
第3節 樹脂と金属のレーザ溶着技術と自動車部材への応用
1.自動車を取り巻く環境の変化―カーボンニュートラルへの対応
2.自動車の軽量化と材料の変遷
3.熱硬化CFRPの課題と熱可塑CFRPの開発
4.自動車構成材料のマルチマテリアル化と異材接合
5.樹脂材料のレーザ溶着技術
6.接合部の強度評価
7.CFRPの接合技術
8.熱可塑性樹脂、CFRTPと金属のレーザ溶着技術
9.樹脂と金属のレーザ溶着技術
9.1 機械的な結合による方法
9.2 化学的な結合による方法
第4節 マルチマテリアルに向けた熱可塑性CFRPと金属の接合
1.部材のマルチマテリアル化の必要性
2.マルチマテリアル化のための接合技術
3.熱可塑性CFRPの融着接合技術
3.1 抵抗融着接合
3.2 超音波融着接合
3.3 高周波誘導融着接合
4.熱可塑性CFRP製リベットを用いたマルチマテリアル化のための機械的接合技術
第5節 自動車のマルチマテリアル化に向けた高強度ウレタン系接着剤
1.異種部材接合における接着剤
2.高強度、高伸長ポリウレタン接着剤
2.1 任意に調整できる物性(弾性率の傾斜機能等)
2.2 温度依存性
2.3 耐久性
3.本技術のウレタン系接着剤の派生展開
3.1 自己接着性
3.2 剛性と制振性
3.3 高強度ウレタン発泡フォームへの展開
4.今後の展開
第6節 接着・接合部の信頼性評価
1.経年劣化による故障発生のメカニズム(ストレス-強度のモデル)
2.所定年数使用後の接着接合部に要求される故障確率確保のために必要な安全率の計算法
2.1 正規分布について
2.2 ストレス(負荷応力)が一定の場合の接着継手の故障確率の確保のために必要な安全率の決定
2.3 ストレス(負荷応力)が変動する場合の接着継手の故障確率の確保のために必要な安全率の決定法
3.接着強度の変動係数実測値
4.寿命試験,加速劣化試験,または疲労試験による劣化後の継手の強度分布および変動係数の測定法および希望故障確率を得るための対策
5.実際の接着構造物の運用により発生する応力xSの変動係数ηSの測定法および必要な故障確率Pf確保の方法
5.1 実構造物の接着層に発生するストレスxSの変動係数ηSの測定法
5.2 希望する故障確率Pfを得るための対策
6.ストレス(負荷荷重)の変動係数の実例
第7節 接着・接合部の耐久性評価と寿命予測法
1.接着接合部の劣化の要因ならびに加速試験と加速係数
1.1 接着接合部劣化の要因
1.2 加速試験と加速係数
1.3 加速試験条件の決定方法
2.アレニウス式(温度条件)による劣化,耐久性加速試験および寿命推定法5-8, 25)
2.1 化学反応速度式と反応次数
2.2 濃度と反応速度および残存率との関係
2.3 材料の寿命の決定法
2.4 反応速度定数と温度との関係
2.5 アレニウス式を用いた寿命推定法
3.アイリングの式による応力,湿度などのストレス負荷条件下の耐久性加速試験および寿命推定法
3.1 アイリングの式を用いた寿命推定法
3.2 アイリング式を用いた湿度に対する耐久性評価法
3.3 Sustained Load Testによる接着継手の温度,湿度,および応力負荷条件下の耐久性評価結果
4.重回帰分析法による接着接合部の寿命予測法
5.実車と同一の接着接合部に対し,市場経年実車と同等の劣化状態を加速試験により作り出す方法
5.1 市場走行実車の接着接合部の残存接着強度測定結果
5.2 実車と同一の被着材に対し,実車と同一接着剤および実車により優れた接着剤aを用いた継手に対し,残存接着強度τr=τlとなる促進劣化条件を求める方法
第8節 金属と樹脂の接合および接合強度評価手法
1.金属/樹脂接合技術
1.1 DRY工法
1.1.1 DLAMP
1.1.2 DLAMP 接合メカニズム
1.1.3 使用可能金属及び接合強度
1.2 WET工法
1.2.1 NMT
1.2.2 NMTエッチング工程
1.2.3 NMT射出成形工程
1.2.4 金属/樹脂直接接合体の界面近傍観察
1.2.5 接合強度及び信頼性試験
2.金属/樹脂接合技術(接着)
2.1 NAT
2.1.1 NAT 接着接合強度
2.1.2 NAT処理 金属/CFRTP(熱可塑性CFRP)熱プレス接合
3.粗面化鍍金による金属/樹脂接合技術
3.1 粗面化Cu鍍金
3.2 粗面化Ni/CB鍍金
4.接合強度特性評価試験方法
4.1 金属/樹脂異種材料接合体の特性評価試験方法
4.2 樹脂/金属異種材料複合体の特性評価試験方法
◇第11章 自動車用新規軽量化材料の開発に向けた 手法とその可能性 ◇
第1節 自動車軽量化に向けたトポロジー最適化
1.密度型トポロジー最適化
1.1 ラグランジュ関数の感度の誘導
1.2 感度に対するフィルタリング処理の導入
1.3 最適性基準法に基づく無次元密度の更新
1.4 密度型トポロジー最適化の計算の流れ
2.密度型トポロジー最適化に関する数値実験
3.レベルセット型トポロジー最適化
3.1 レベルセット型トポロジー最適化における式展開
3.2 レベルセット型トポロジー最適化の計算の流れ
4.レベルセット型トポロジー最適化に関する数値実験
第2節 トポロジー手法を用いた接合位置最適化による車体性能の向上
1.最適化モデル
1.1 スポット打点位置最適化
1.2 構造用接着剤塗布位置最適化
2.慣性リリーフを用いた剛性解析
2.1 慣性リリーフを用いた車体剛性解析
2.2 慣性リリーフを用いたトポロジー手法による最適スポット打点位置
2.3 慣性リリーフを用いたトポロジー手法による最適構造用接着剤塗布位置
3.走行解析を用いた最適化
3.1 走行解析による荷重の同定
3.2 走行解析結果を用いたスポット打点位置最適化
3.3 走行解析結果を用いた構造接着剤塗布位置最適化
第3節 「折紙工学」による軽くて強いを中心とする自動車材料開発の可能性
1.展開収縮可能な折紙構造
1.1 厚板折畳構造
1.2 エネルギー吸収折紙構造
1.3 折紙構造の双安定性を利用した防振器
1.4 折紙構造のスプリングバック特性を利用した防振器
2.軽くて剛な折紙構造
2.1 トラスコア
2.2 ATCPの誕生―輸送箱としての優秀性
2.3 ATCP輸送箱から誕生した新しい固有周波数制御技術
2.4 折紙工法で得られる高アスペクトコア付き平板の優れた遮音特性
3.切紙ハニカム