★提携会社 書籍のご案内

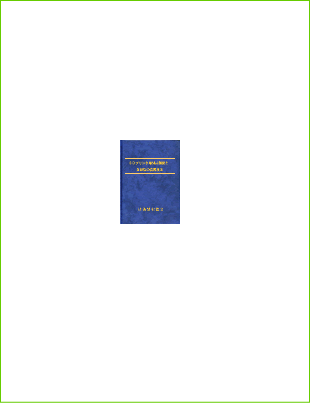

3Dプリンタ用 材料開発と造形物の高精度化
定価 ¥ 44,000(税込)
販売価格 ¥ 44,000(税込)
商品番号:dg0038
ISBN: 978-4-86104-793-0
下記から目次項目単位を選択し、購入目次を設定願います。
■発刊日:2020年5月15日
■販売者:パテントテック社
■出版社:株式会社 技術情報協会
■資料体裁:A4版、469頁
■オンデマンド印刷版(上製本ではありません)
★ 最終製品の量産化に向けての 「コスト低減」 と 「高精度化」 の両立は?
★ 材料と造形技術との相性、造形物の面粗さ・ガス焼け・ウェルドライン等への対策!
■本書のポイント
●各種造形材料の造形特性と用途展開
・樹脂粉末:ポリアミド、チタン酸カリウム繊維、 形状記憶ポリウレタン、PPフィラメント、シリコーン、軟質フィラメント
・金属、無機材料:ニッケル基合金、アルミニウム合金、アルミナ、セラミック、砂型用、
●造形物の高精度化テクニックと後処理
・樹脂・金属積層・セラミック造形機の特性、使い方
・造形シミュレーションの精度向上
・造形物の面粗さ、ガス焼け、ウェルドラインの解消
・サポート材の除去、平滑化、透明化、めっき処理
●試作品から最終製品への適用拡大に向けた課題と対策
・ダイレクト生産、納期短縮・コストダウンの実績は?
・導入へのハードル、課題と対策
●各種産業分野での応用事例、新規材料開発事例
・成型用金型、自動車、航空宇宙、医療機器分野での活用
・CFRP部材、ポーラス金属、超硬合金の開発
■執筆者(敬称略)
アルケマ(株) | 宮保 淳 | (株)ACR | 野口 宏 |
大塚化学(株) | 稲田 幸輔 | (株)金星 | 飯田 浩 |
ダウ・東レ(株) | 小渕 喜一 | 愛知工業大学 | 山田 章 |
ダウ・東レ(株) | 石神 直哉 | 愛知工業大学 | 武田 亘平 |
ホッティーポリマー(株) | 田鍋 史生 | 長野県工業技術総合センター | 堀 剛 |
キョーラク(株) | 湯浅 亮平 | (株)東レリサーチセンター | 村岡 正義 |
ナノダックス(株) | 佐藤 勲昌 | 呉工業高等専門学校 | 山脇 正雄 |
日立金属(株) | 桑原 孝介 | 産業技術総合研究所 | 高辻 利之 |
名古屋工業大学 | 渡辺 義見 | カンタツ(株) | 大嶋 英司 |
東洋アルミニウム(株) | 橋詰 良樹 | (地独)東京都立産業技術研究センター | 千葉 浩行 |
(地独)大阪産業技術研究所 | 木村 貴広 | 矢崎総業(株) | 漆畑 卓朗 |
豊橋技術科学大学 | 武藤 浩行 | 富士ゼロックス(株) | 藤井 雅彦 |
豊橋技術科学大学 | Tan Wai Kian | 京葉ケミカル(株) | 根本 達広 |
豊橋技術科学大学 | 横井 敦史 | 埼玉県産業技術総合センター | 南部 洋平 |
東京工業大学 | 浜野 凌平 | (地独)東京都立産業技術研究センター | 竹村 昌太 |
東京工業大学 | 横井 理史 | 帝人ナカシマメディカル(株) | 井上 貴之 |
東京工業大学 | 生駒 俊之 | (株)リコー | 渡邉 政樹 |
群栄化学工業(株) | 永井 康弘 | みずほ情報総研(株) | 鶴岡 茉佑子 |
(株)ストラタシス・ジャパン | 三森 幸治 | 名古屋市立大学 | 田上 辰秋 |
兵庫県立工業技術センター | 兼吉 高宏 | 名古屋市立大学 | 尾関 哲也 |
(株)J・3D | 高関 二三男 | SOLIZE Products(株) | 岩井 正義 |
丸紅情報システムズ(株) | 丸岡 浩幸 | (株)十川ゴム | 井田 剛史 |
ヘガネスジャパン(株) | 宮本 政博 | ブラザー工業(株) | 矢澤 宏明 |
(株)松浦機械製作所 | 吉田 光慶 | 東京工業大学 | 中川 佑貴 |
東京大学 | 小西 邦昭 | 名古屋大学 | 鈴木 飛鳥 |
東京大学 | 湯本 潤司 | 栃木県産業技術センター | 高岩 徳寿 |
第一セラモ(株) | 和田 誠 | 大阪大学 | 小笹 良輔 |
白銅(株) | 石塚 伸一 | 大阪大学 | 石本 卓也 |
(株)写真化学 | 法貴 哲夫 | 大阪大学 | 中野 貴由 |
アズワン(株) | 于 涛 | 冨士ダイス(株) | 内藤 寛道 |
香川県産業技術センター | 横田 耕三 | TOTO(株) | 安藤 正美 |
JSR(株) | 澤田 安彦 |
◇第1章 3Dプリンタ用樹脂系材料の造形特性と用途展開◇
第1節 粉末床溶融結合 (PBF) 造形向けポリアミド材料
1.3Dプリンター技術としての粉末床溶融結合 (PBF) 造形
2.樹脂粉末を用いる PBFの概要
3.PBF材料としてのポリアミド
4.PBFに最適な長鎖脂肪族ポリアミド
5.ポリアミド11とポリアミド12の違い
6.アルケマ社のPBF向けポリアミド材料
6.1 Orgasol(オルガソル) Invent Smooth (OIS)
6.2 Rilsan(リルサン)Invent Natural (RIN)
おわりに
第2節 3Dプリンタ用チタン酸カリウム繊維の活用
1.チタン酸カリウム繊維:ティスモ、樹脂複合材料:ポチコンに関して
2.MEX方式3Dプリンタ用チタン酸カリウム繊維入り材料の作成
3.MEX方式3Dプリンタでの造形
4.結果と考察
4.1 造形安定性評価
4.2 物性評価
4.3 摩擦摩耗特性
5.今後の展開
6.まとめ
第3節 3Dプリンター用シリコーンゴムの開発(仮)
1.背景
2.シリコーンゴム
2.1 シリコーンゴムの基礎知識
2.2 液状シリコーンゴム
3.LAM(液体積層法:Liquid Additive Manufacturing)の開発
4.3Dプリンター用シリコーンゴムの開発
4.1 3Dプリンター用シリコーンゴムの調製
4.2 3Dプリンター用シリコーンゴムの物性
5.使用例
6.オプション
7.まとめ
第4節 3Dプリンタ用軟質フィラメントの用途、加工条件
1.3Dプリンタ用軟質フィラメントの用途
1.1 建材分野
1.2 医療分野
1.3 教育分野
1.4 スポーツ関連分野
1.5 機械関連の分野
1.6 自動車関連の分野
1.7 今後の用途展開
1.8 その他、
2.3Dプリンタ用軟質フィラメントの加工条件
2.1 フィラメント作成時の条件
2.2 FDM方式3Dプリンタのフィラメント供給方法による分類と用語の説明および軟質フィラメントに適した供給方式
2.2.1 ダイレクトドライブ方式
2.2.2 ボーデンタイプ方式
2.3 3Dプリンタによる造形時の条件
2.4 軟質フィラメントを造形する場合の3Dプリンタのメンテナンス時等の注意点
2.5 独自の軟質フィラメント専用3Dプリンタについて
第5節 3Dプリンタ用形状記憶ポリウレタンの特徴
1.形状記憶フィラメント「SMP55」
1.1 3Dプリンター用フィラメント「SMP55」の特徴
1.2 形状記憶ポリマーの特性
1.3 形状変形特性・形状記憶特性
1.4 エネルギー散逸特性
1.5 ガス透過率の温度依存性
1.6 SMPの成型性
2.形状記憶特性を活かした3Dプリントでの活用例
2.1 4Dプリンティングへの応用
2.2 ポストプロセスカスタマイゼーション
おわりに
第6節 造形性に優れたPPフィラメントの用途展開
1.環境負荷軽減の流れ
2.開発経緯
3.フィラメント技術(収縮制御技術)
4.特長
5.フィラメント物性(ペレット代表物性値)
6.造形時の留意点
7.主な用途
8.今後の展開
◇第2章 3Dプリンタ用金属系材料の造形特性と用途展開 ◇
第1節 金属積層用材料の特徴と新材料開発事例
1.積層造形法の分類と用いられる材料
2.高強度高耐食MPEAの積層造形への適用
3.超高耐食ニッケル基合金の適用
おわりに
第2節 ヘテロ凝固機構により高造形性・高強度を実現する3Dプリンティング用金属粉末
1.凝固マップとヘテロ凝固理論
2.ヘテロ凝固核粒子の選定と金属粉末の作製
3.ヘテロ凝固核粒子を添加した3Dプリンティング
4.まとめ
第3節 積層造形用アルミニウム合金粉末の特徴と応用
1.アルミニウム合金の積層造形について
2.金属積層造形用粉末の要求特性
3.アルミニウム合金粉末の製造技術
4.球状アルミニウム合金粉末の特性
5.アルミニウム合金の積層造形における課題
6.積層造形に適したアルミニウム合金の開発
7.金属粉末の安全な取扱い
8.今後の展開
第4節 アルミニウム合金粉末を用いたレーザ積層造形技術の開発
1.レーザ積層造形における造形条件の最適化
1.1 本研究におけるレーザ照射条件の最適化方法
1.2 レーザ照射条件の探索プロセス
2.造形体の特性評価
2.1 造形体の金属組織
2.2 造形体の機械的性質
3.熱処理による造形体の機械的性質の制御
3.1 造形体の組織の変化
3.2 造形体の機械的性質の変化
おわりに
◇ 第3章 3Dプリンタ用無機系材料の造形特性と用途展開◇
第1節 3Dプリンタ用セラミック材料の粉末設計
はじめに
1.粉末集積化と材料開発
1.1 粉末設計の重要性
1.2 付加製造技術のための粉末デザイン
1.2.1 レーザ吸収性が制御された粉末の開発
1.2.2 流動性の高い粉末の開発
1.2.3 複合材料の造型が可能な粉末の開発
1.3 粉末の集積化技術
2.付加製造技術への展開
2.1 レーザ吸収性が制御された粉末の開発
2.2 流動性の高い粉末の開発
2.3 複合材料の造型が可能な粉末の開発
おわりに
第2節 水硬性アルミナを用いた三次元積層造形
はじめに
1.3DPの原理と歴史
2.アルミナの三次元積層造形
2.1 α-アルミナについての研究報告
2.2 水硬性アルミナの水和硬化反応
3.水硬性アルミナの造形
3.1 原料調製と積層造形
3.2 硬化処理
3.3 焼結
まとめ
第3節 砂型用3Dプリンタ材料の応用展開
1.砂型用3D積層造形技術の概要
1.1 実用化されている装置および方法
1.2 3D積層造形技術用鋳物砂の現状と新技術
1.3 高流動性コーテッドサンド技術
1.4 砂型積層造形用バインダ
1.4.1 バインダに求められる特性
1.4.2 フランケミストリー
1.4.3 フランバインダ
1.4.4 硬化反応メカニズム
2.高流動性コーテッドサンドを使用した3D積層造形技術
2.1 鋳造への展開
3.まとめ
◇第4章 樹脂系材料を造形する3Dプリンタ装置の使用法と応用展望◇
第1節 樹脂系3Dプリンタの現状と今後の展望
1.積層造形の活用領域
2.積層造形の導入メリット
3.積層造形の品質保証
4.DfAM (積層造形向き設計)
5.今後の応用展望について
第2節 ゴム用3Dプリンタの活用
◇第5章 金属3Dプリンタ装置の使用法と応用展望 ◇
第1節 金属3Dプリンタの現状と今後の展望
はじめに
1.金属3Dプリンタの現状
1.1 海外の金属3Dプリンタマーケット
1.2 国内の金属3Dプリンタマーケット
1.3 金属3Dプリンタ粉末
1.4 金属3Dプリンタの技術の進歩
1.5 金属3Dプリンタサービスビューロ
1.6 3Dデータの普及
1.7 変わりゆく海外での設計思想
2.金属3Dプリンタの課題
2.1 コスト
2.2 造形サイズ
2.3 表面粗さ
2.4 造形速度
2.5 寸法精度
2.6 サポート材
2.7 残留応力
2.8 金属材料の種類
2.9 ノウハウ
2.10 内部欠陥
2.11 疲労強度
2.12 異方性
2.13 粉末の再利用
2.14 アスペクト比
2.15 レーザーの寿命
3.金属3Dプリンタの今後の展望
3.1 最新の金属3Dプリンタ開発動向
3.2 金属3Dプリンタが期待されている分野
3.3 4Dプリンタ
3.4 新技術とのコラボレーション
3.5 ソフトウェアの進化
4.まとめ
第2節 材料押出方式金属3Dプリンタ特徴と造形例
はじめに
1.Desktop Metal社と製品の概要
1.1 Desktop Metal社の概要
1.2 Desktop Metal社の製品概要
2.材料押出方式採用「StudioTM(スタジオ)」システムの特徴
2.1 BMD法の概要と特徴
3.「StudioTM」システムの活用事例
3.1 適する活用の分野
3.2 北米先行ユーザーでの活用事例
おわりに
第3節 バインダージェット方式による造形物の高精度化
はじめに
1.金属バインダージェット方式の起源
2.造形原理
3.熱処理とクリーニング
4.材料
5.利用事例
まとめ
第4節 ハイブリッド金属3Dプリンターによる高精度造形
はじめに
1.ハイブリッド金属3Dプリンターとは
2.ハイブリッド金属3Dプリンターの切削技術のメリット
2.1 段ずらし加工における面粗度向上
2.2 造形物の上面切削機能
2.3 後加工基準面の作成
3.アプリケーション例
3.1 プラスチック成形用金型
3.2 部品
4.まとめ
第5節 高精細3DプリンターRECILSの応用展開
はじめに
1.1次元規制液面型3DプリンターRECILS
1.1 1次元規制液面型3次元積層造形技術
1.2 造形物表面の金属コーティング
2.ポリマー・金属ハイブリッド構造のテラヘルツ電磁波制御素子への応用
2.1 RECILSと金属コーティングの活用によるテラヘルツ導波管の作製
2.2 導波管構造のアレイ化によるテラヘルツハイパスフィルターの作製
3.まとめ
第6節 粉末射出成形(PIM)技術を応用した3D積層造形
1.3D積層造形
1.1 3D積層造形の特徴
1.2 金属およびセラミックス材料の3D積層造形
2.PIM技術
2.1 粉末射出成形(PIM)の特徴
2.2 PIMプロセス
3.PIM技術を応用した3D積層造形
3.1 3D積層造形用コンパウンドの創製
3.2 3D積層造形用コンパウンド技術
3.3 3D積層造形の応用例
4.今後の展開
5.おわりに
第7節 金属3Dプリンターを用いた金属製品の造形技術と活用事例
はじめに
1.金属3Dプリンター導入の背景
2.「ProXシリーズ」の強み
3.当社の造形におけるサービス体制
4.金属積層造形のルール
5.サポート材について
6.金属3Dプリンターに必要なデータ
7.金属3Dプリンターの活用事例(メリット)
8.金属3Dプリンターに関する誤解(デメリット)と今後の課題
9.金属3Dプリンターの展望
◇ 第6章 無機系材料を造形する3Dプリンタ装置の使用法と応用展望 ◇
第1節 (株)エスケーファインのセラミックス造形技術
はじめに
1.各種3D造形法の特徴
2.高精細光造形法の描画技術
3.セラミックス造形法の概要
3.1 セラミックス造形装置の構成と動作の概要
3.2 セラミックス粉末をフィラー分散した造形
3.3 セラミックス造形品の脱脂・焼結処理
4.高精細セラミックス造形事例
5.セラミックス造形の品質評価
5.1 焼結体の収縮率
5.2 焼結密度
5.3 抗折強度
5.4 焼結体のSEM観察
6.セラミックス造形の展開
第2節 Lithoz社の高性能セラミック光硬化造形技術のご紹介
はじめに
1. LCMとは何か?
2. 高密度・高性能セラミックのためのスマートテクノロジー
3. LCMが市場を牽引する主な要因、アーリーアダプター、最先端イノベーション
4. セラミック鋳造用原型
5. 医療および歯科用途
6. 工業および機械用途
7. 小型化
8. 連続生産への規模拡大:製造過程の信頼性と生産性
9. 結論
第3節 DLP式光造形法による3次元積層造形セラミックスの作製
はじめに
1.光造形法について
2.光硬化セラミックスラリーの調製と特性
2.1 光硬化セラミックスラリーの調製
2.2 光硬化セラミックスラリーの単層硬化試験
3.セラミックスの造形および焼結体の作製
3.1 下面照射型DLP式光造形法によるセラミックスの造形
3.2 セラミックス造形体の焼成
4.セラミックス造形焼結体の事例
5.セラミックス造形の今後の展開
◇ 第7章 製造工程、生産技術に対する3Dプリンティングの活用◇
第1節 最終品の量産を可能にする3Dプリンタの活用法
はじめに
1.ラピッドプロトタイピングから最終製品へ
2.技術革新による3Dプリンタの進化
2.1 HP
2.2 Carbon
2.3 Markforged
3.Carbonプリンタについて
3.1 Carbonの沿革
3.2 Carbonのデジタルマニュファクチャリング
3.2.1 Carbonプリンタの造形原理
3.2.2 Carbonのサポート体制
3.3 Carbonの採用事例
3.3.1 自動車
3.3.2 航空宇宙
3.3.3 消費財
4.最終品への適用拡大に向けた課題
4.1 3Dプリンタの活用シーン
4.2 3Dプリンタからデジタルマニュファクチャリングへ
4.2.1 材料種の拡大と低コスト化
4.2.2 新技術に適応した組織スキルのアップグレード
おわりに(長期的展望)
第2節 金属3Dプリンタによる自動車部品の低コスト造形技術
はじめに
1.導入の経緯
1.1 3Dプリンタ導入後の目も当てられない実体
1.1.1 立ちはだかる□30mmの壁
1.1.2 金属粉末削減指令
1.2 オープンパラメータへの挑戦
1.2.1 新しく見つけた金属粉末
1.2.1 やっと手に入れた造形パラメータ(焼結レシピ)
2.ターボ開発の納期短縮、コストダウン実績
2.1 コストダウン、納期短縮
3.独自造形パラメータ(焼結レシピ)での作品紹介
3.1 超小型ディーゼルエンジン用ターボ部品
3.2 小型ディーゼルエンジン用ターボ部品
3.3 その他の部品
最後に
第3節 3Dプリンタによるダイレクト生産の導入と課題
はじめに
1.ダイレクト生産の導入
1.1 ダイレクト生産に用いている3Dプリンタ
1.2 3Dプリンタよる最終製品の設計を行う上での留意点
1.3 3Dプリンタの造形品質と最終製品への利用における対策について
1.4 最終製品としてのコストの低減方法
1.5 最終製品を生産する際における生産速度の課題
2.ダイレクト生産による効果
2.1 開発速度の向上
2.2 市場最適化の高速化
2.3 ダイレクト生産の導入が効果的な領域
3.今後の課題
3.1 二次処理の課題
3.2 二次処理の課題
おわりに
◇ 第8章 3Dプリンタ造形物の物性、強度、品質評価◇
第1節 3Dプリンタ製生分解構造物の分解に伴う強度特性の評価
はじめに
1.熱溶解積層方式の3Dプリンタとポリ乳酸
1.1 熱溶解積層方式
1.2 ポリ乳酸製の構造物
2.ポリ乳酸の分解進行と強度低下
2.1 ポリ乳酸の分解と強度低下
2.2 3Dプリンタによって作製したポリ乳酸製構造物の浸漬に伴う強度特性の変化
3.強度特性の評価方法
3.1 強度特性の評価
3.2 微小サイズの引張試験片を用いた機械的特性の評価
3.2.1 試験片の形状と作製方法
3.2.2 引張試験による機械的特性の評価
3.2.3 浸漬試験片、引張試験の準備、質量の変化
3.2.4 破断試験片の観察
4.ポリ乳酸の分解進行に伴う機械的特性
4.1 試験片
4.2 未浸漬試験片の機械的特性
4.3 浸漬試験片の機械的特性
4.4 浸漬に伴う試験片の重量変化
4.5 破断試験片の観察
4.6 3Dプリンタによるポリ乳酸製構造物の浸漬に伴う強度低下のメカニズム
5.まとめ
第2節 3Dプリンタ用樹脂の耐候性評価
はじめに
1.実験方法
1.1 試験機及び試験方法
1.2 試料
1.3 試料の評価方法
1.3.1 表面観察
1.3.2 色差評価
1.3.3 引張強度試験
2.実験結果及び考察
2.1 表面観察
2.2 色差評価
2.3 引張強度試験
2.4 キセノン試験とメタルハライド試験の相関
おわりに
第3節 インクジェット式プリンタで造形した樹脂製品の分析
はじめに
1.3Dプリンタ関連の分析評価
2.3Dプリンタ造形物の分析例
2.1 試料
2.2 機械特性評価
2.3 硬化度
2.4 寸法安定性
2.5 残存成分、臭気の把握
2.6 残塗布方法により機械特性が異なる原因は?
3.おわりに
◇第9章 3Dプリンティングによる造形物の高精度化、加工条件の設定◇
第1節 3DプリンタによるCFRP積層造形技術
はじめに
1.FRP用3Dプリンタの基本技術
1.1 積層プロセス
1.2 積層造形物の機械的強度
1.3 CFRPフィラメント材料
1.4 既存のテープによる成形技術との比較
2.3Dプリンタの特徴と応用分野
3.代表的な3Dプリンタと技術動向
3.1 XYZ軸駆動型3Dプリンタ
3.2 ロボットアームを利用した3Dプリンタ
3.3 シートを用いて積層造形を実現する3Dプリンタ
むすび
第2節 3Dスキャナと3Dプリンタの連携による造形物の高精度化
はじめに
1.クローズドループエンジニアリング
2.評価用器物
2.1 評価用器物の基本
2.2 評価用器物(a)
2.3 評価用器物(b)
2.3.1 評価用器物(b)の設計
2.3.2 評価用器物(b)の測定
2.4 評価用器物(c)
2.4.1 評価用器物(c)の設計
2.4.2 評価用器物(c)の測定
3.3Dプリンタ造形物の補正検証
第3節 光造形装置としても直描露光装置としても使える1台2役の高速/高精度な3Dプリンタの開発
1.はじめに(開発の背景)
2.SPACE ARTの特長
3.SPACE ARTの構造・仕様・回路パターン形成プロセスフロー
3.1 直描露光装置(電子回路パターン/レジストパターン形成)仕様
3.2 光造形装置(3Dプリンタ)仕様
4.光学エンジンの構成
5.本装置の機能・性能
5.1 直描露光装置(電子回路パタンやレジスト形成)の機能・性能
5.2 光造形装置(3Dプリンタ)の機能・性能
6. おわりに(今後の展開)
第4節 金属積層造形用シミュレーションの精度向上
はじめに
1.金属積層造形用シミュレーションの現状
1.1 金属積層造形用シミュレーションの目的
1.2 金属積層造形用シミュレーションの機能
1.2.1 金属積層造形用シミュレーションの解析方法
1.2.2 金属積層造形用シミュレーションソフトウェアの一般的機能
2.金属積層造形用シミュレーションの課題
2.1 金属積層造形用シミュレーション結果と実造形現象の比較
2.2 金属積層造形用シミュレーションの課題
3.今後の金属積層造形用シミュレーションの精度向上のための取組
おわりに
第5節 積層造形品の平滑化
はじめに
1.複合レーザ平滑化プロセスの検証
1.1 短パルスレーザによる凸部除去
1.2 酸化層およびデブリの除去
1.3 溶融平滑化
2.積層造形品の複合レーザ平滑化
2.1 被照射材料
2.2 複合プロセスによる積層造形品の平滑化加工
3.まとめ
第6節 高い表現力を実現するボクセルベースのデータフォーマットFAV
はじめに
1.ボクセルによる3D表現とFAVフォーマット
2.ボクセルベースデータの効用と活用
3.ボクセルデータの課題と対応
第7節 3Dプリンタ/サポート除去洗浄技術 美しい造形品との出会い
はじめに
1.蝋と造形物
2.境界面
3.二次汚染
4.水と油
5.別な作用
6.対比
7.サポート材の質量
8.EXTRIPPER
9.進化系
10.環境問題など
終わりに
◇第10章 後処理・後加工技術◇
第1節 Material Jetting 造形物の後処理
はじめに
1.実験方法
1.1 造形物表面の観察・分析
1.2 残存サポート樹脂除去方法の検討
1.3 透明化の検討
1.3.1 浸漬による透明化
1.3.2 研磨による透明化
1.4 塗装手順の検討
1.5 めっき処理の検討
2.結果及び考察
2.1 造形物の表面状態
2.2 残存サポート樹脂の除去
2.3 透明化の検討結果
2.3.1 浸漬による透明化
2.3.2 研磨による透明化
2.4 塗装手順の検討結果
2.5 めっき処理の検討結果
3.まとめ
第2節 樹脂系3D造形物のめっき処理
はじめに
1.ナイロン樹脂AMモデルへのめっき前処理方法の検討
1.1 前処理方法その1:無電解めっき
1.2 前処理方法その2:塗装
2.塗装後の電気めっき
3.意匠性を考慮しためっき条件の検討
4.意匠性を考慮したAM立体モデルの作製
5.おわりに
◇ 第11章 各産業分野における3Dプリンタの活用事例◇
第1節 電子ビーム積層造形法による医療製品の開発
はじめに
1.人工関節に要求される機能
1.1 関節動作の再建
1.2 生体適合性
1.3 荷重の支持
2.新規人工関節の設計と製造法
2.1 多孔体設計
2.2 積層造形法の選択
3.製品化プロセス
3.1 薬機法
3.2 造形条件
3.3 材料組成
3.4 生物学的安全性
3.5 HIP(Hot Isostatic Press)処理
3.6 後処理
3.7 ロット検査
4.今後の展望
4.1 大腿骨ステムへの応用
4.2 カスタムメイド化
4.3 材料の改質
第2節 インクジェット式3Dプリンターによる骨置換型人工骨の成形
はじめに
1.結合剤噴射法(Binder Jetting)による骨の造形
2.高精度・高強度人工骨を目指した造形法
2.1 新規BJ方式の概要
2.2 3Dプリント人工骨の特性評価
3.人工骨の生体適応性
3.1 細胞培養実験
3.2 ラットin vivo実験
4.生体から見た人工骨の反応と応用展開
4.1 バイオマテリアルとしての人工骨の立ち位置と課題
4.2 3Dプリント人工骨の生体反応と応用展開
第3節 医療における3Dプリンタ(AM装置)の活用動向
1.医療における3D プリンタの実用事例
1.1 ユーザごとにカスタマイズした製品の生産
1.2 複雑な構造の造形
1.3 設計・試作・検証サイクルの短縮
2.再生医療分野で注目が集まる3Dバイオプリンタ
3.医療における3Dプリンタ普及への取組と課題
3.1 規制環境
3.2 コスト
3.3 応用先
第4節 3Dプリンター技術によるオーダーメイド医療の可能性と3Dバイオプリンターを用いた錠剤の調製
はじめに
1.現在市販されている3Dプリンター錠剤(SPRITAM)
2.医薬品製造に3Dプリンター技術を適用することのメリット
3.医療機関における3Dプリンターの導入
4.3Dバイオプリンターを用いた錠剤の調製
5.その他の種類の3Dプリンターを用いた錠剤の調製
おわりに
第5節 航空宇宙分野への3Dプリンタの活用
1.航空機における搭載事例
1.1 エアバス事例
1.2 ボーイング x ストラタシスによるインフィニティービルド共同開発事例
1.3 中国東方航空事例
1.4 ニュージーランド航空事例(Bruce Parton, COOへのインタビュー)
1.5 エティハド航空事例
1.6 商用ロケットAtrasV事例
1.7 月有人宇宙船事例(米国)
第6節 3Dプリンターによる自動車補給部品の直接造形
はじめに
1.自動車最終部品・補給部品製造に求められる3Dプリンターの条件
1.1 材料特性、生産性、コスト、信頼性
1.2 Multi Jet Fusionの特長
2. Multi Jet Fusion方式の自動車最終部品・補給部品適用事例
2.1 自動車カスタムパーツ、少量生産車事例
2.2 自動車補給部品事例
2.3 日本国内での取り組み事例
3.SOLIZE Productsの取り組み
3.1 国内初のHP Digital Manufacturing Network参加企業
3.2 データ処理の取り組み 充填率の向上による部品単価の低減
3.3 ポストプロセスの工法開発、自動化、効率化
3.4 品質管理の取り組み
4.自動車補給部品への適用に向けて
4.1 補給部品適用コンサルティングサービス
4.2 部品選定
4.3 材料評価、性能評価試験
4.4 生産準備
4.5 補給部品の3Dプリンターでの直接造形
4.6 適用範囲の拡大、DfAM(Design for Additive Manufacturing)の取り組み
5.自動車補給部品への適用が期待できるその他の3Dプリンターの工法
5.1 イノベーションへの期待
5.2 DLP方式光造形
5.3 パウダーベッド方式 レーザー金属3Dプリンター
5.4 HP Metal Jet(インクジェット バインダー結合方式)
6.まとめ
第7節 3Dプリンタによる自動車用部材の試作開発・生産への活用
はじめに
1.自動車用部材の試作開発・生産への3Dプリンタ活用の背景
1.1 デジタルエンジニアリングツールとしての3Dプリンタ
1.2 3Dプリンタによる試作品の評価検証事例
2.自動車用部品の試作開発や生産における3Dプリンタの活用
2.1 試作開発や生産における3Dプリンタ活用の意義
2.2 自動車用部品の生産ラインにおける3Dプリンタの活用事例
2.3 3Dプリンタの金型への活用と試作開発
3.3Dプリンタでの自動車部品DDMの可能性と課題
第8節 電車保守分野での3Dプリンタの活用事例
第9節 開発の効率化,期間短縮を実現する3Dプリンタの活用事例
はじめに
1.開発現場の目標とする状態
1.1 開発現場で早期活用するための条件
2.3Dプリンタ活用環境の例
2.1 対象の開発製品
2.2 3Dプリンタの選定
2.3 運用の仕組みの構築
3.3Dプリンタ活用による効果
3.1 試作期間の短縮
3.2 開発費用の削減
3.3 開発者の評価時間の確保
3.4 デジタルモールドの活用
4.開発における3Dプリンタ活用の今後
◇ 第12章 3Dプリンティングによる新しい材料開発◇
第1節 3Dプリンティングで製造されたCFRP部材の高強度化
はじめに
1.3Dプリンティングで製造されたCFRP部材
1.1. CFRP部材の3Dプリンティング
2.炭素繊維挟み込みによるCRFP部材の3Dプリンティング
2.1 炭素繊維の挟込みによる強化
2.2 繊維と樹脂との加熱接着
2.3 マイクロ波加熱による加熱接着の簡略化
2.4 マイクロ波加熱における課題
3.レーザー加熱を複合したCFRP部材の高強度化
3.1 レーザーによる加熱接着
3.2 適用可能な樹脂色
3.3 CFRP部材内の炭素繊維のレーザー加熱
4.3DプリンティングされるCFRP部材の展望
第2節 金属3Dプリンタによる鉄鋼材料の造形条件の確立
はじめに
1.種々のエネルギー密度の表現
1.1 体積エネルギー密度(Volumetric Energy Density)
1.2 ライン造形におけるエネルギー密度
1.3 Deposited energy density
2.マルエージング鋼を例とした種々エネルギー密度による整理
2.1 実験条件
2.2 P・v-1に基づく整理
2.3 P/v1/2に基づく整理
2.4 P・v-1/2の優位性と問題点
3.まとめ
第3節 3Dプリンタを用いたポーラス金属作製
はじめに
1.ポーラス金属作製に関する研究手法
1.1 CADによるポーラス構造の設計
1.2 造形条件変更によるポーラス金属の作製
1.3 造形条件変更によるポーラス金属の密度制御
2.結果と考察
2.1 CADによるポーラス構造の設計
2.2 造形条件変更によるポーラス金属の作製
2.3 造形条件変更によるポーラス金属の密度制御
3.おわりに
第4節 金属3Dプリンタによる結晶方位制御に基づく高機能積層造形材料の開発
はじめに
1.金属3Dプリンタによる組織・原子配列制御
1.1 金属粉末の溶融/凝固と単結晶・方向制御結晶・多結晶の形成
1.2 溶融池形状と組織・原子配列の関係
2.金属3Dプリンタ特有の高機能性積層造形組織を有する材料の創製
2.1 等方性/異方性材質の形成と制御
2.2 積層方向への繊維状結晶集合組織の形成と制御
2.3 積層方向に平行なラメラ組織の形成と制御
おわりに
第5節 バインダージェット3Dプリンタによる超硬合金の製作
はじめに
1.バインダージェット方式の積層造形機の仕組みおよび特徴
2.バインダージェット方式の積層造形機を用いた超硬合金の製作
2.1 造粒粉末粒子の特性
2.2 超硬合金の積層造形および焼結
2.3 焼結体の加工
2.4 評価方法
2,5 積層造形法および粉末冶金法で製作した試料の特性値
2.6 積層造形法および粉末冶金法で製作した打抜きパンチによる寿命評価
3.まとめ
第6節 3D積層造形によるセラミックス構造部材の開発
はじめに
1.3D積層造形技術の半導体製造装置用セラミックス構造部材への応用
1.1 半導体製造装置用セラミックス構造部材
1.2 3D積層造形技術開発の狙い
2.セラミックス3D積層造形技術の開発
2.1 粉末積層造形を用いた反応焼結SiC部材の開発
2.2 スラリー積層造形を用いたアルミナ部材の作製
おわりに